Home> Company News> 3 Pump Hydraulic Setup: Why, When and What To Use
- AddressNorth Tan Street, Jinan,Shandong
- Factory Address123 Ubi Ave 3 #12-30 Frontier Singapore 408867
- Worktime9:00-18:00(Beijing time)
- Phone(Working Time)86 0531-8299 9952
A 3 pump hydraulic setup is a type of hydraulic system that uses three pumps to power different functions. These setups are commonly used in industrial machinery and heavy equipment, where multiple functions need to be performed simultaneously. The importance of using a 3 pump hydraulic setup is to ensure that the system operates efficiently and effectively, with each pump performing a specific task. In this article, we will discuss the different types of pumps used in a 3 pump hydraulic setup and their functions. We will also highlight the advantages of using a 3 pump hydraulic setup and its relevance in various applications.
Why Use a 3 Pump Hydraulic Setup?
A 3 pump hydraulic setup offers a number of advantages over other hydraulic setups, such as a single pump setup or a dual pump setup. One of the primary benefits is increased system efficiency. By using multiple pumps, the load can be distributed more evenly, resulting in less wear and tear on individual components and a more reliable system overall.
In addition to increased efficiency, a 3 pump hydraulic setup can also provide greater flexibility. With multiple pumps, it's possible to adjust the flow and pressure of each pump to match the specific needs of the system. This means that the system can be customized to provide optimal performance for a wide range of applications.
Another advantage of a 3 pump hydraulic setup is redundancy. With multiple pumps in place, the system can continue to operate even if one pump fails. This can be particularly important in applications where downtime is costly or where safety is a concern.
Of course, there are also some potential drawbacks to using a 3 pump hydraulic setup. One of the biggest concerns is cost. Because multiple pumps are required, a 3 pump hydraulic setup can be more expensive to install and maintain than other hydraulic systems. Additionally, the increased complexity of the system can make troubleshooting more difficult in the event of a problem.
Despite these potential challenges, a 3 pump hydraulic setup is often the best choice for applications that require high efficiency, flexibility, and reliability. By carefully considering the needs of the system and working with a qualified hydraulic system designer, it's possible to create a customized 3 pump hydraulic setup that meets your specific needs and provides optimal performance.
When to Use a 3 Pump Hydraulic Setup?
A 3 pump hydraulic setup is often used in situations where there is a need for multiple hydraulic systems to work simultaneously. These systems may require different levels of pressure, volume, or flow rate, and a single pump or dual pump setup may not be able to meet these requirements efficiently.
For instance, in industrial machinery, a 3 pump hydraulic setup can be used to power different systems such as the steering, brakes, and lifting mechanisms. These systems require different pressure levels and flow rates to function effectively. A 3 pump setup ensures that each system has the necessary pressure and flow rate to function optimally, leading to increased efficiency and productivity.
Similarly, in heavy equipment such as excavators and bulldozers, a 3 pump hydraulic setup can be used to power different systems such as the hydraulic cylinders, motor, and brake system. Again, each system requires different levels of pressure and flow rate to function efficiently, and a 3 pump setup ensures that these requirements are met.
In general, a 3 pump hydraulic setup is ideal for situations where multiple hydraulic systems need to be powered simultaneously and require varying levels of pressure and flow rate. It is a versatile and reliable setup that ensures optimal performance and efficiency in a range of applications.
What Are the Components of a 3 Pump Hydraulic Setup?
A 3 pump hydraulic setup consists of three separate hydraulic pumps, each with its own dedicated function. These pumps work together to provide the necessary hydraulic power to operate various systems and equipment. The components of a 3 pump hydraulic setup include:
-
Pumps: The three pumps in a 3 pump hydraulic setup each serve a different function. The first pump is usually the main or primary pump that provides hydraulic power to the system. The second pump is usually an auxiliary or secondary pump that provides additional power to the system when needed. The third pump is usually a backup pump that is used in case one of the other pumps fails.
-
Valves: Valves are used to control the flow of hydraulic fluid between the pumps and the system being operated. They are also used to direct the flow of fluid to different parts of the system.
-
Reservoirs: Hydraulic fluid reservoirs are used to store and regulate the flow of hydraulic fluid. They are usually located near the pumps and provide a ready supply of fluid for the system.
-
Hoses: Hoses are used to transport hydraulic fluid between the pumps, valves, and system being operated. They are typically made of reinforced rubber or other durable materials to withstand the high pressure and temperature of hydraulic fluid.
Each component in a 3 pump hydraulic setup plays a critical role in ensuring the proper functioning of the system. Any malfunction or failure of these components can result in the system not working as intended, which can cause serious safety risks and expensive repairs. Therefore, it is important to use high-quality components and perform regular maintenance to ensure the system is working optimally.
How to Set Up a 3 Pump Hydraulic System?
Setting up a 3 pump hydraulic system can be a complex process, but with the right tools and instructions, it can be done efficiently and effectively. Here is a step-by-step guide on how to set up a 3 pump hydraulic system:
-
Determine the hydraulic flow rate requirements: Before setting up a 3 pump hydraulic system, it's important to know the hydraulic flow rate requirements of your machinery or equipment. This will help you choose the appropriate pumps for your system.
-
Select the appropriate pumps: Choose the pumps based on the hydraulic flow rate requirements of your machinery or equipment. Ensure that the pumps you choose are compatible with each other and the rest of the hydraulic system components.
-
Install the pumps: Mount the pumps in the appropriate location in your machinery or equipment. Ensure that the pumps are securely mounted and that they have enough clearance for proper operation.
-
Connect the pumps: Connect the pumps to the hydraulic system components, including the valves, reservoirs, and hoses. Ensure that the connections are tight and secure to prevent any leaks.
-
Install the valves: Install the valves in the hydraulic system to regulate the flow of hydraulic fluid. Choose the appropriate valves based on the requirements of your machinery or equipment.
-
Connect the valves: Connect the valves to the hydraulic system components, including the pumps, reservoirs, and hoses. Ensure that the connections are tight and secure to prevent any leaks.
-
Install the reservoirs: Install the reservoirs in the appropriate location in your machinery or equipment. Ensure that the reservoirs are securely mounted and that they have enough clearance for proper operation.
-
Connect the reservoirs: Connect the reservoirs to the hydraulic system components, including the pumps, valves, and hoses. Ensure that the connections are tight and secure to prevent any leaks.
-
Install the hoses: Install the hoses in the appropriate location in your machinery or equipment. Ensure that the hoses are securely mounted and that they have enough clearance for proper operation.
-
Connect the hoses: Connect the hoses to the hydraulic system components, including the pumps, valves, and reservoirs. Ensure that the connections are tight and secure to prevent any leaks.
-
Test the system: Once the hydraulic system is fully installed, test it for proper operation. Check for any leaks or other issues and address them as needed.
-
Label the system: Label each component of the hydraulic system for easy identification and maintenance.
Overall, setting up a 3 pump hydraulic system requires careful planning, proper installation techniques, and regular maintenance to ensure optimal performance. By following these steps, you can set up a reliable and efficient hydraulic system for your machinery or equipment.
Maintenance and Troubleshooting Tips for a 3 Pump Hydraulic System
Like any hydraulic system, a 3 pump hydraulic setup requires regular maintenance to ensure it functions correctly. Here are some essential maintenance and troubleshooting tips to keep in mind when working with a 3 pump hydraulic system.
Maintenance
-
Check fluid levels: The first step in maintaining a 3 pump hydraulic system is to check the fluid levels regularly. Low fluid levels can cause damage to the pump and the hydraulic system.
-
Change filters: Filters in the system should be checked and changed on a regular basis to prevent contaminants from entering the system and causing damage to the components.
-
Inspect for leaks: Regular inspections should be conducted to identify and address leaks in the system. Leaks can lead to reduced system performance, increased downtime, and costly repairs.
-
Lubricate components: Lubricating the components of the 3 pump hydraulic system is crucial to ensure smooth and efficient operation. Make sure to use the recommended lubricants and follow the manufacturer's guidelines.
-
Replace worn components: Worn components can cause system inefficiencies and even lead to system failure. Replace any worn or damaged components as soon as possible to prevent further damage.
Troubleshooting
-
Identify the problem: The first step in troubleshooting a 3 pump hydraulic system is to identify the problem. Some common issues include low pressure, leaks, and system overheating.
-
Check fluid levels: Low fluid levels can cause problems in the system, so make sure to check the fluid levels and top up as necessary.
-
Check filters: Clogged filters can cause a range of issues, so check and change the filters if necessary.
-
Check for leaks: Leaks can cause damage to the system and reduce its performance. Inspect the system for leaks and address them promptly.
-
Inspect components: Worn or damaged components can cause problems in the system. Inspect the components and replace any that are worn or damaged.
Recommended maintenance schedule
The maintenance schedule for a 3 pump hydraulic system depends on the specific system and its usage. However, it is generally recommended to follow the manufacturer's guidelines and perform regular maintenance tasks, such as fluid checks, filter changes, and inspections, on a monthly or quarterly basis.
Best practices for maintaining a 3 pump hydraulic system
Here are some best practices to keep in mind when maintaining a 3 pump hydraulic system:
-
Use the recommended fluids and lubricants: The manufacturer's guidelines should be followed when selecting fluids and lubricants for the system.
-
Keep the system clean: A clean system will help prevent contaminants from entering the system and causing damage to the components.
-
Address problems promptly: Promptly addressing problems in the system can prevent further damage and reduce downtime.
-
Regularly inspect the system: Regular inspections can identify potential problems before they become major issues.
-
Follow the manufacturer's guidelines: The manufacturer's guidelines should be followed for all maintenance tasks to ensure the system functions correctly and to prevent voiding the warranty.
By following these maintenance and troubleshooting tips, you can keep your 3 pump hydraulic system functioning optimally and reduce downtime.
Conclusion
A 3 pump hydraulic setup is a powerful and versatile hydraulic system that offers a range of benefits over other setups, such as single or dual pump setups. With multiple pumps working in tandem, a 3 pump hydraulic system can deliver high flow rates and pressure levels that are necessary for heavy-duty applications such as industrial machinery or heavy equipment.
To set up a 3 pump hydraulic system, it is important to have a clear understanding of the components involved, including the pumps, valves, reservoirs, and hoses. Regular maintenance is also essential to ensure proper functioning of the system, and troubleshooting common issues that may arise can help prevent downtime and costly repairs.
Overall, a 3 pump hydraulic setup is an excellent choice for those seeking a reliable and efficient hydraulic system that can handle even the most demanding applications. With proper maintenance and care, a 3 pump hydraulic system can provide many years of reliable service, making it a worthwhile investment for businesses and industries that rely on hydraulic equipment.
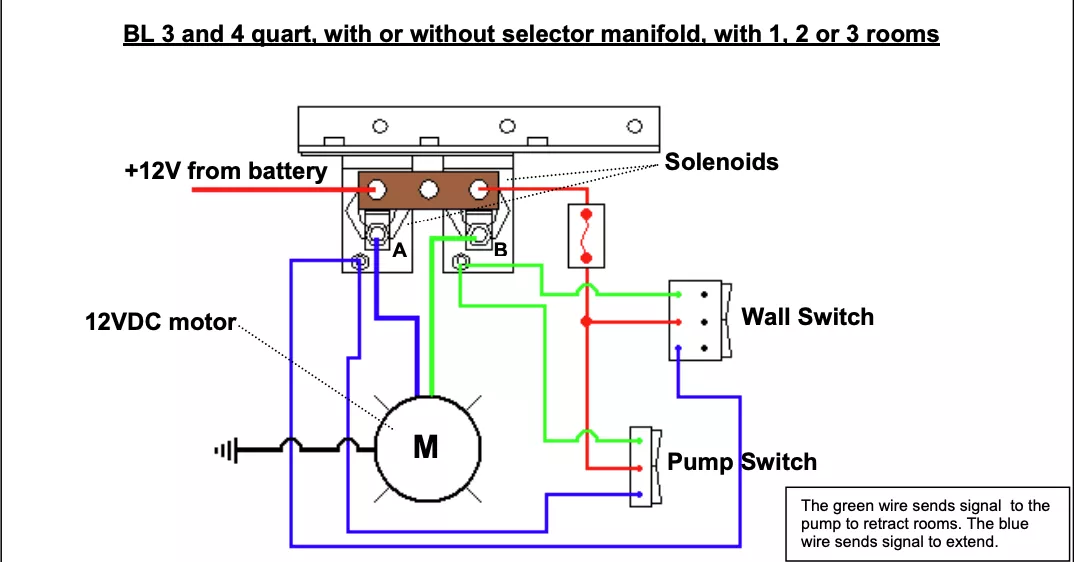
Sure, I can provide a list of frequently asked questions (FAQs) about 3 pump hydraulic setups and their answers:
Q: What is a 3 pump hydraulic setup? A: A 3 pump hydraulic setup is a type of hydraulic system that uses three pumps to operate different functions in a machine or system. Each pump is dedicated to a specific task and helps to optimize the system's performance.
Q: Why use a 3 pump hydraulic setup? A: Using a 3 pump hydraulic setup can provide a number of benefits, including improved efficiency, increased reliability, and better control over different functions of the machine or system. It can also help to extend the lifespan of the hydraulic components.
Q: What types of pumps are used in a 3 pump hydraulic setup? A: The three types of pumps commonly used in a 3 pump hydraulic setup are gear pumps, vane pumps, and piston pumps. Each pump has its own unique characteristics and advantages, depending on the specific needs of the machine or system.
Q: What are some examples of applications that require a 3 pump hydraulic setup? A: A 3 pump hydraulic setup is often used in heavy equipment and industrial machinery, such as excavators, cranes, and bulldozers. It can also be used in agricultural equipment, such as tractors and combines, as well as in automotive systems, such as power steering and braking.
Q: How do you set up a 3 pump hydraulic system? A: Setting up a 3 pump hydraulic system involves careful planning and installation to ensure that each pump is properly connected and aligned with the rest of the system. It is important to follow the manufacturer's instructions and to work with a qualified hydraulic technician to ensure proper installation.
Q: How do you maintain a 3 pump hydraulic system? A: Proper maintenance of a 3 pump hydraulic system involves regular inspection and cleaning of the pumps, reservoirs, and hoses, as well as checking fluid levels and replacing filters as needed. It is important to follow the manufacturer's recommended maintenance schedule and to work with a qualified technician for any repairs or upgrades.
Q: What are some common issues that may arise in a 3 pump hydraulic system? A: Common issues that may arise in a 3 pump hydraulic system include leaks, low pressure, and excessive noise or vibration. Troubleshooting these issues may involve checking for loose connections, inspecting the pumps and hoses for damage, and adjusting fluid levels or pressure settings as needed.
Q: How can you troubleshoot a 3 pump hydraulic system? A: Troubleshooting a 3 pump hydraulic system involves identifying the specific issue and then using a systematic approach to diagnose and repair the problem. This may involve checking for leaks, inspecting the pumps and hoses for damage, and adjusting fluid levels or pressure settings as needed. It is important to work with a qualified technician to ensure proper troubleshooting and repairs.