Home> Company News> 2 Stage Hydraulic Pump Adjustment – Make Sure It's Set Properly
- AddressNorth Tan Street, Jinan,Shandong
- Factory Address123 Ubi Ave 3 #12-30 Frontier Singapore 408867
- Worktime9:00-18:00(Beijing time)
- Phone(Working Time)86 0531-8299 9952
Understanding 2-Stage Hydraulic Pumps
Hydraulic systems play a crucial role in various industrial and manufacturing applications, such as heavy machinery, construction equipment, and even amusement park rides. One essential component of hydraulic systems is the hydraulic pump, which is responsible for generating the necessary fluid power to drive the system's components.
A 2-stage hydraulic pump is a type of hydraulic pump that provides two levels of pressure in a single pump. These pumps can generate high pressure for demanding applications and low pressure for lighter loads, making them a versatile option for various industrial needs.
The way a 2-stage hydraulic pump works is by using two gears with different sizes that are located within the same housing. As the pump rotates, the gears move the fluid from the inlet to the outlet, generating the necessary pressure levels. When the pump is operating at a lower pressure, only the smaller gear is engaged. As the pressure increases, the larger gear is engaged, providing additional power.
The benefits of using a 2-stage hydraulic pump in your hydraulic system are numerous. The ability to generate different pressure levels allows for a broader range of applications to be handled by a single pump, saving space and reducing the need for multiple pumps. Additionally, the dual-stage design provides better efficiency, reducing energy consumption and saving on operating costs. In short, a 2-stage hydraulic pump can improve the overall performance and efficiency of a hydraulic system, making it an attractive option for industrial applications.
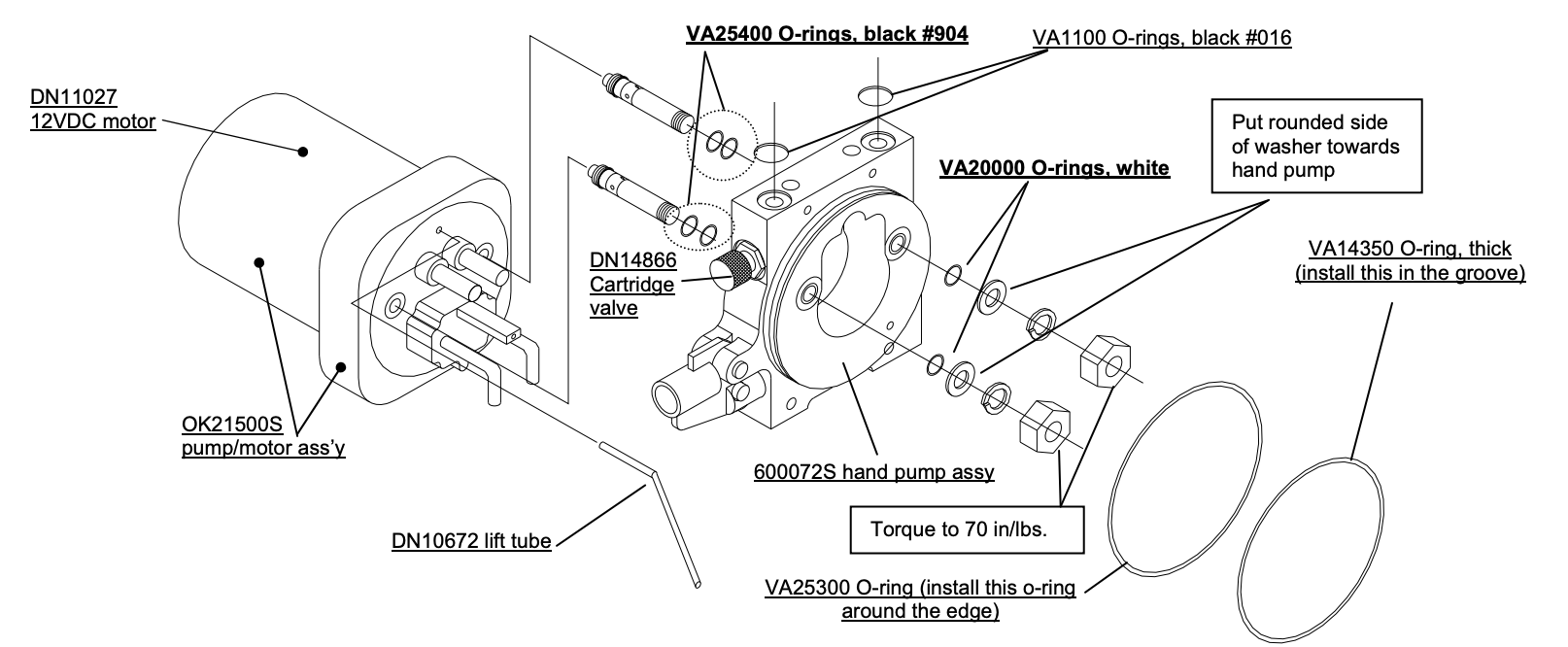
Reasons for Adjusting 2-Stage Hydraulic Pumps
2-stage hydraulic pumps are used in a variety of applications to increase the efficiency and power of hydraulic systems. However, to ensure optimal performance, it is important to adjust them properly. Improper adjustment can lead to a range of issues, including reduced system performance and increased wear and tear on system components.
One common reason for adjusting a 2-stage hydraulic pump is to optimize its pressure output. If the pump is not adjusted correctly, it may not deliver the necessary pressure to power the system, leading to decreased performance and efficiency. Similarly, if the pressure is too high, it can cause excess wear and tear on system components, potentially leading to costly repairs.
Another reason for adjusting a 2-stage hydraulic pump is to optimize its flow rate. The flow rate of a hydraulic pump determines how quickly hydraulic fluid is circulated through the system. If the flow rate is too low, it can lead to slow system response times and decreased performance. On the other hand, if the flow rate is too high, it can put excess strain on system components, potentially leading to premature failure.
Proper adjustment of a 2-stage hydraulic pump is essential to ensure optimal system performance and longevity. By understanding the reasons for adjusting a 2-stage hydraulic pump, users can take the necessary steps to ensure their system is functioning at its best.
Techniques for Proper Adjustment
Properly adjusting a 2-stage hydraulic pump is crucial to ensuring optimal performance and preventing damage to the pump and other components in the hydraulic system. Here are some steps for adjusting a 2-stage hydraulic pump to ensure it is working as efficiently as possible:
-
Gather the necessary tools and equipment. Before you begin adjusting the pump, make sure you have all the necessary tools and equipment on hand. This may include a pressure gauge, a wrench or socket set, and a user manual for the specific pump you are working on.
-
Determine the optimal pressure settings. The pressure settings for a 2-stage hydraulic pump will vary depending on the specific application and system requirements. Refer to the pump's user manual or consult with a hydraulic systems expert to determine the optimal pressure settings for your particular system.
-
Adjust the low-pressure relief valve. The first stage of a 2-stage hydraulic pump is responsible for generating low-pressure flow. Use a pressure gauge to measure the low-pressure output, and adjust the low-pressure relief valve as necessary to achieve the desired pressure setting.
-
Adjust the high-pressure relief valve. The second stage of a 2-stage hydraulic pump generates high-pressure flow. Use a pressure gauge to measure the high-pressure output, and adjust the high-pressure relief valve as necessary to achieve the desired pressure setting.
-
Test the pump's performance. Once you have adjusted the pressure relief valves, it is important to test the pump's performance to ensure that it is operating as expected. Monitor the pressure readings over a period of time to ensure they remain within the desired range, and make adjustments as necessary.
By following these steps, you can ensure that your 2-stage hydraulic pump is adjusted properly and functioning efficiently. However, it is important to note that adjusting a hydraulic pump can be a complex process, and it is recommended to consult with a hydraulic systems expert to ensure that the adjustment is done correctly and safely.
Troubleshooting 2-Stage Hydraulic Pump Adjustment
Even with the proper adjustment techniques, issues may arise during the adjustment of a 2-stage hydraulic pump. Some common problems and issues that can arise during 2-stage hydraulic pump adjustment include:
-
Excessive noise: This can be caused by several factors, including loose fittings or air in the system. If the noise persists after adjustment, further investigation may be required.
-
System overheating: Overheating can be caused by several factors, including low oil levels or incorrect fluid viscosity. If the system continues to overheat after adjustment, additional troubleshooting may be necessary.
-
Slow system response: This can be caused by a number of issues, including restricted fluid flow or worn components. If the response time does not improve after adjustment, further investigation may be necessary.
-
Inconsistent pressure: This can be caused by a number of factors, including a worn or damaged relief valve. If pressure inconsistencies continue after adjustment, further troubleshooting may be necessary.
When troubleshooting 2-stage hydraulic pump adjustment issues, it is important to follow a systematic approach. This may include checking fluid levels, inspecting components for damage or wear, and reviewing the system's specifications to ensure that all components are properly matched. It may also be necessary to consult with a hydraulic system expert to help diagnose and resolve any issues.
Safety Precautions for 2-Stage Hydraulic Pump Adjustment
Adjusting a 2-stage hydraulic pump requires caution and proper safety measures to ensure that the process is safe and effective. Failure to adhere to safety protocols can result in serious injury or damage to the hydraulic system. Here are some safety precautions to take when adjusting a 2-stage hydraulic pump:
-
Wear Personal Protective Equipment (PPE): It is essential to wear protective gear such as safety goggles, gloves, and hearing protection when adjusting a 2-stage hydraulic pump. This equipment can protect you from injury caused by high-pressure fluid, debris, or loud noise.
-
Turn off the Power: Before adjusting the pump, it is crucial to turn off the power supply to the hydraulic system. This prevents the pump from accidentally starting while the adjustment is in progress.
-
Relieve Pressure: It is important to relieve pressure from the hydraulic system before adjusting the 2-stage hydraulic pump. This can be done by slowly opening the pressure relief valve or disconnecting the pump from the system and allowing it to drain.
-
Use Proper Tools: Only use appropriate tools for adjusting the 2-stage hydraulic pump. This includes hydraulic pressure gauges and wrenches that are specifically designed for hydraulic systems. Using the wrong tools can damage the pump and cause injury.
-
Be Aware of Moving Parts: During the adjustment process, it is essential to be mindful of moving parts such as the drive shaft and couplings. Ensure that your hands and clothing do not get caught in these moving parts, which can cause injury.
-
Follow Manufacturer's Instructions: Always follow the manufacturer's instructions for adjusting the 2-stage hydraulic pump. This ensures that the adjustment is done correctly and safely.
By following these safety precautions, you can ensure that adjusting your 2-stage hydraulic pump is done safely and effectively.
Maintenance for 2-Stage Hydraulic Pumps
Proper maintenance is essential for ensuring the longevity and optimal performance of 2-stage hydraulic pumps. By following a regular maintenance schedule, you can reduce the likelihood of system failures and extend the life of your equipment. Here are some tips for maintaining your 2-stage hydraulic pump:
-
Check fluid levels regularly: It is important to check the fluid levels in your hydraulic pump regularly. Low fluid levels can cause your pump to overheat and potentially fail. Make sure to check the fluid level and top it off if necessary.
-
Change the fluid regularly: Contaminated fluid can cause significant damage to your hydraulic pump. Make sure to change the fluid at regular intervals to ensure that it is clean and free of debris.
-
Check for leaks: Leaks can cause your hydraulic pump to lose pressure and ultimately fail. Make sure to check your pump for any leaks and repair them as soon as possible.
-
Inspect the components: Regularly inspecting the components of your hydraulic pump can help you identify potential issues before they become major problems. Check for signs of wear and tear, and replace any damaged components.
-
Follow the manufacturer's recommendations: The manufacturer's recommendations for maintenance should always be followed to ensure the proper functioning of your hydraulic pump. Make sure to refer to the owner's manual for any specific maintenance instructions.
-
Keep the pump clean: Dirt and debris can cause your hydraulic pump to fail. Make sure to keep the pump clean and free of any obstructions.
By following these maintenance tips, you can ensure that your 2-stage hydraulic pump operates at optimal levels and lasts for many years. Regular maintenance can also save you money in the long run by reducing the need for costly repairs and replacements.
Applications for 2-Stage Hydraulic Pumps
2-stage hydraulic pumps find use in a wide range of industries and applications due to their ability to deliver high pressure and flow rates, making them ideal for heavy-duty tasks. Here are some common industries and applications that benefit from the use of 2-stage hydraulic pumps:
-
Construction - 2-stage hydraulic pumps are commonly used in heavy construction equipment such as excavators, backhoes, and bulldozers. These machines require high-pressure hydraulic systems to power their various hydraulic components, including their hydraulic motors, cylinders, and valves.
-
Agriculture - 2-stage hydraulic pumps are also widely used in agricultural machinery such as tractors and harvesters. They are used to power implements such as plows, tillers, and cultivators, as well as to raise and lower the machines' booms and arms.
-
Mining - Mining equipment, including drills, shovels, and excavators, often rely on 2-stage hydraulic pumps for their hydraulic systems. The pumps provide the necessary pressure to power the machines' various components, such as hydraulic motors, cylinders, and valves.
-
Aerospace - 2-stage hydraulic pumps are used in the aerospace industry to power hydraulic systems in aircraft. The pumps provide the pressure necessary to operate landing gear, flaps, and other hydraulic components.
-
Manufacturing - 2-stage hydraulic pumps are used in manufacturing processes that require high-pressure hydraulic systems, such as metal stamping and plastic injection molding machines.
-
Marine - Boats and ships require hydraulic systems to power their steering mechanisms, winches, and other components. 2-stage hydraulic pumps are used to provide the necessary pressure to operate these systems.
Overall, 2-stage hydraulic pumps are versatile and find use in a wide range of industries and applications where high pressure and flow rates are required. Their reliability and efficiency make them a popular choice among professionals in these fields.
Advancements in technology are constantly driving innovation in the hydraulic industry, and 2-stage hydraulic pumps are no exception. As manufacturers continue to explore new materials, designs, and manufacturing techniques, the future of 2-stage hydraulic pump technology looks promising.
One area of development is in the use of smart technologies, which can improve the accuracy and efficiency of 2-stage hydraulic pumps. Smart sensors and controllers can monitor pump performance and automatically adjust pressure and flow rates to optimize system performance. This can help reduce energy consumption and prevent premature wear and tear on system components.
Another area of focus is on improving the durability and lifespan of 2-stage hydraulic pumps. Advancements in materials science and manufacturing techniques are making it possible to develop pumps that can withstand even harsh operating conditions. For example, new coatings and surface treatments can help protect pump components from wear and corrosion, while new manufacturing techniques can create stronger and more resilient pump housings.
There is also ongoing research into alternative power sources for hydraulic pumps. As environmental concerns continue to grow, manufacturers are exploring ways to power pumps using renewable energy sources such as solar or wind power. This could help reduce the carbon footprint of hydraulic systems and make them more environmentally friendly.
Overall, the future of 2-stage hydraulic pump technology is exciting, with ongoing developments that promise to improve performance, efficiency, and durability. As the industry continues to evolve, we can expect to see even more advancements that push the boundaries of what is possible with hydraulic technology.